
Our in-house Sheet Metal Fabrication offers customers a high quality, bespoke service.
Quite simply, sheet metal fabrication comprises numerous industrial processes that we use to turn a variety of metals into sheets of the desired shape and thickness, which then go on to be used in a huge array of end products.
If you would like more information regarding our Sheet Metal Fabrication processes, please Contact Us today.


Laser Profile & Cutting
Laser cutting is a precise method of cutting a design out of a sheet. The laser head follows a specific path to produce the desired profile.

A focused beam strikes the material with such heat that it melts or even vaporises the material; the beam can then pierce through the workpiece. The cutting process begins when the laser moves along the part, melting the material as it moves. Laser cutting is a highly accurate and fast process.
The TruLaser 3030 is a cutting-edge piece of fibre laser technology. It uses CO2 lasers which cuts the sheet using oxygen, nitrogen and compressed air to combine high performance with cut quality that is second to none. The laser is robust, reliable and versatile, providing extremely smooth cutting edges to a variety of different materials.
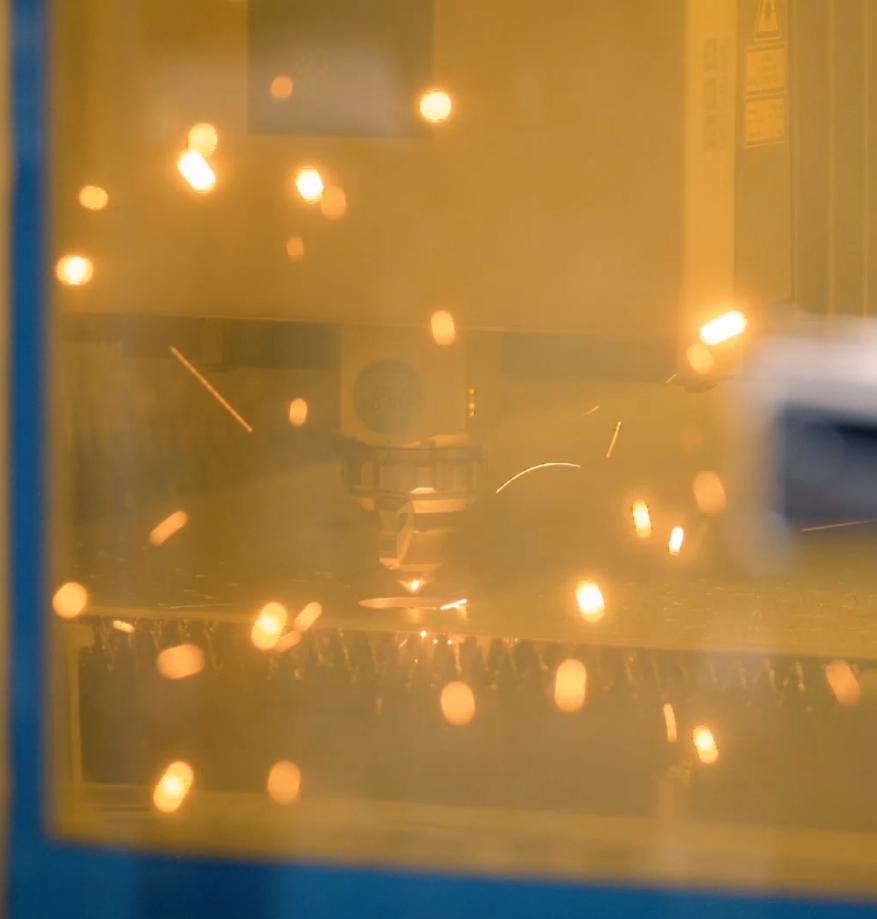


Punch
Punching is the process of a tool being forced through a sheet of metal at high velocity, causing the sheet to become perforated, profiled, or formed.

Dimple, vent, louvre and forming are examples of different punched features which can be manufactured from the Amada Vipros 2510 King.
The Amada Vipros 2510 King Turret Punching Machine is operated through a FANUC Series 18-P control unit; this large format machine is equipped with 3 clamps for securing the workpiece.
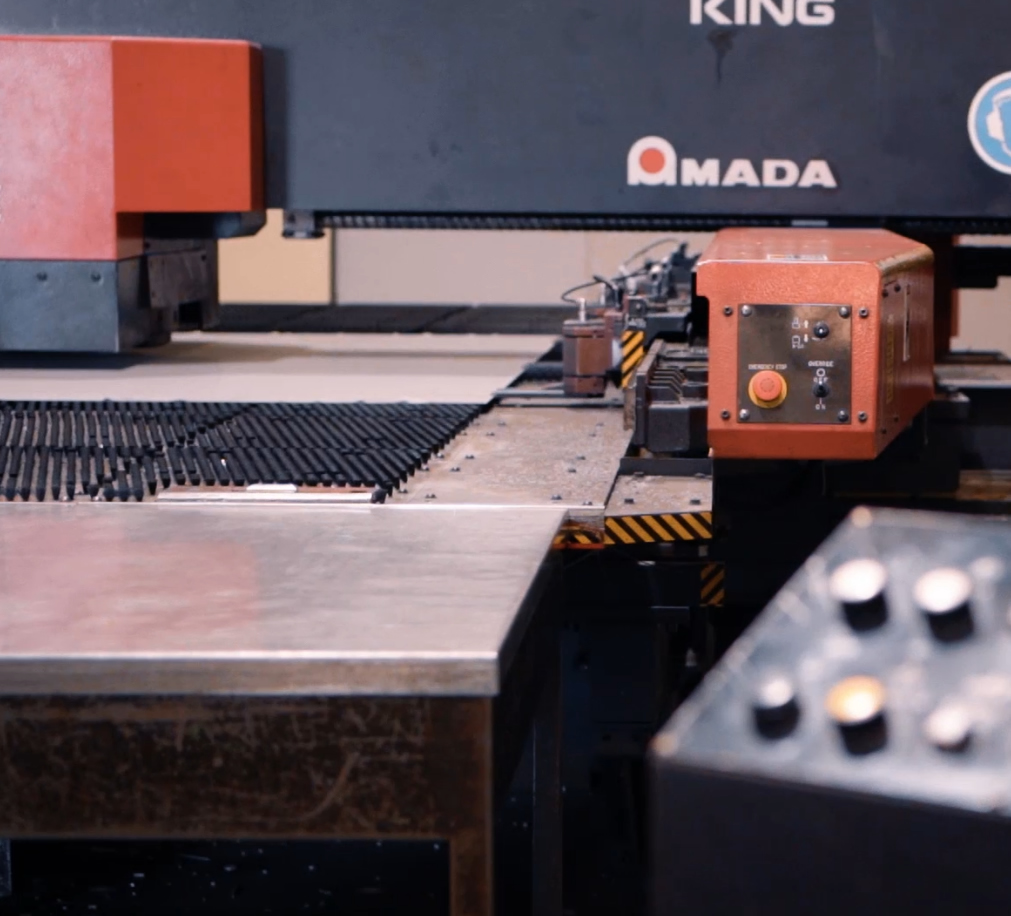

Bending
Bending is the manufacturing process by which sheet metals can be deformed by applying force to the subject.

This causes it to bend at an angle and form the intended shape. Bending uses a press brake, which allows small intricacies to be folded. It also allows a vast variety of shapes to be created for many different products that are used day-to-day.
The Amada HFE3i series is the latest evolution in hydraulic drive press brakes. The 3i series features new additions to improve productivity, including an innovative multi-touch screen interface. The precision of the press brake allows high quality products to be manufactured here at Lazenby’s.
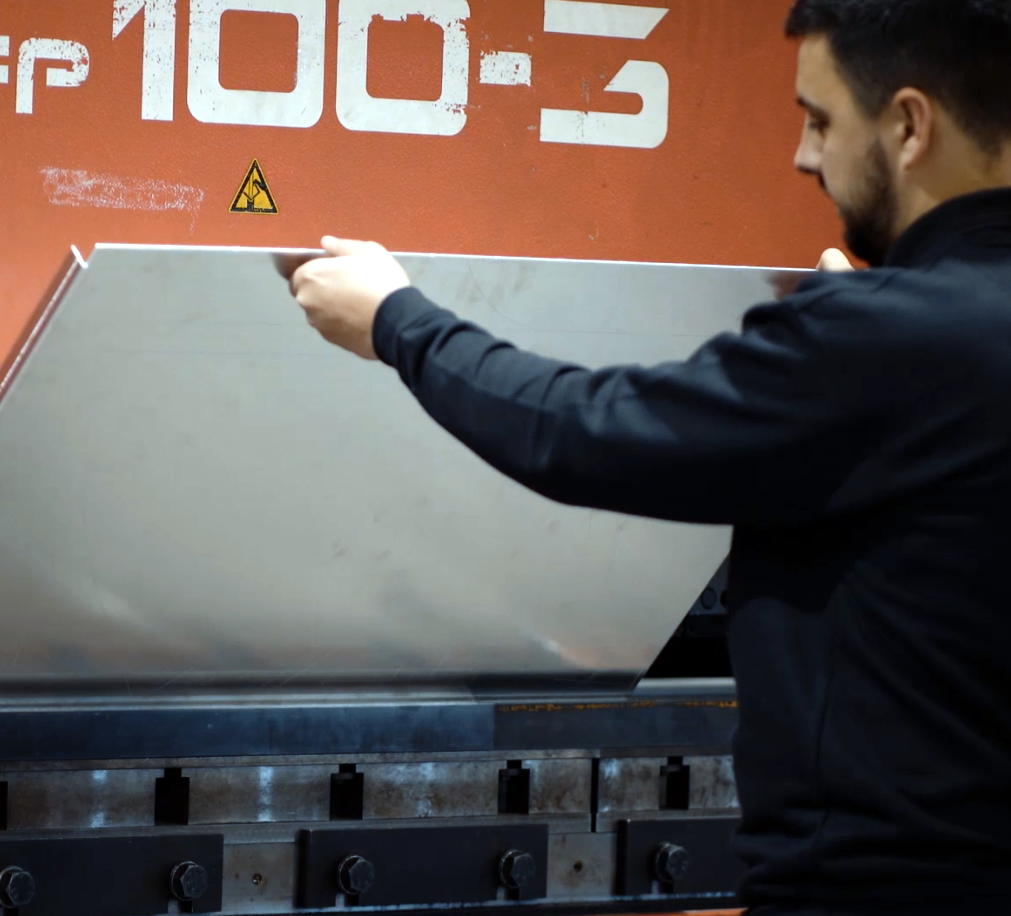


Welding
Welding is a fabrication process which joins parts together to produce an assembled component by using electricity to heat and melt the parts together and allowing them to cool, causing fusion.

Lazenby’s offer a range of welding solutions including MIG (Metal Insert Gas), TIG (Tungsten Insert Gas) and spot welding.
MIG and TIG are the most common types of welding; the difference between MIG and TIG is the way the arc is used. MIG welding uses a feed wire that constantly moves through the gun to create the spark, which then melts to form the weld. TIG welding uses long rods to fuse two metals directly together. Spot welding is a type of electric resistance welding used to weld various sheet metal products through a process in which contacting metal surface points are joined by the heat obtained from resistance to electric current. All our experienced and qualified welders deliver the highest standard, ensuring the highest quality of work is produced, ready for the next stage of manufacturing.
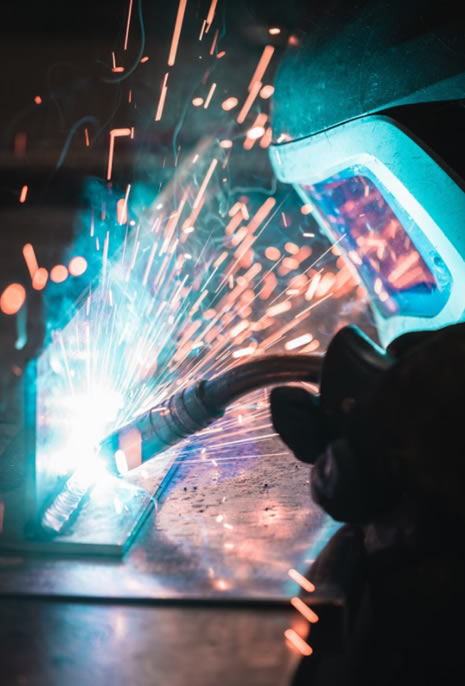

Powder Coating
Powder Coating is a type of finish coating that is applied as a free-flowing dry powder to give components the finished look.

The powder is a mixture of ground particles of resin and pigment which is applied electrostatically and is then cured under heat between 200⁰C and 240⁰C.
Different types of finishes are available for your product; our team can help advise you on the best solution for your intended application.
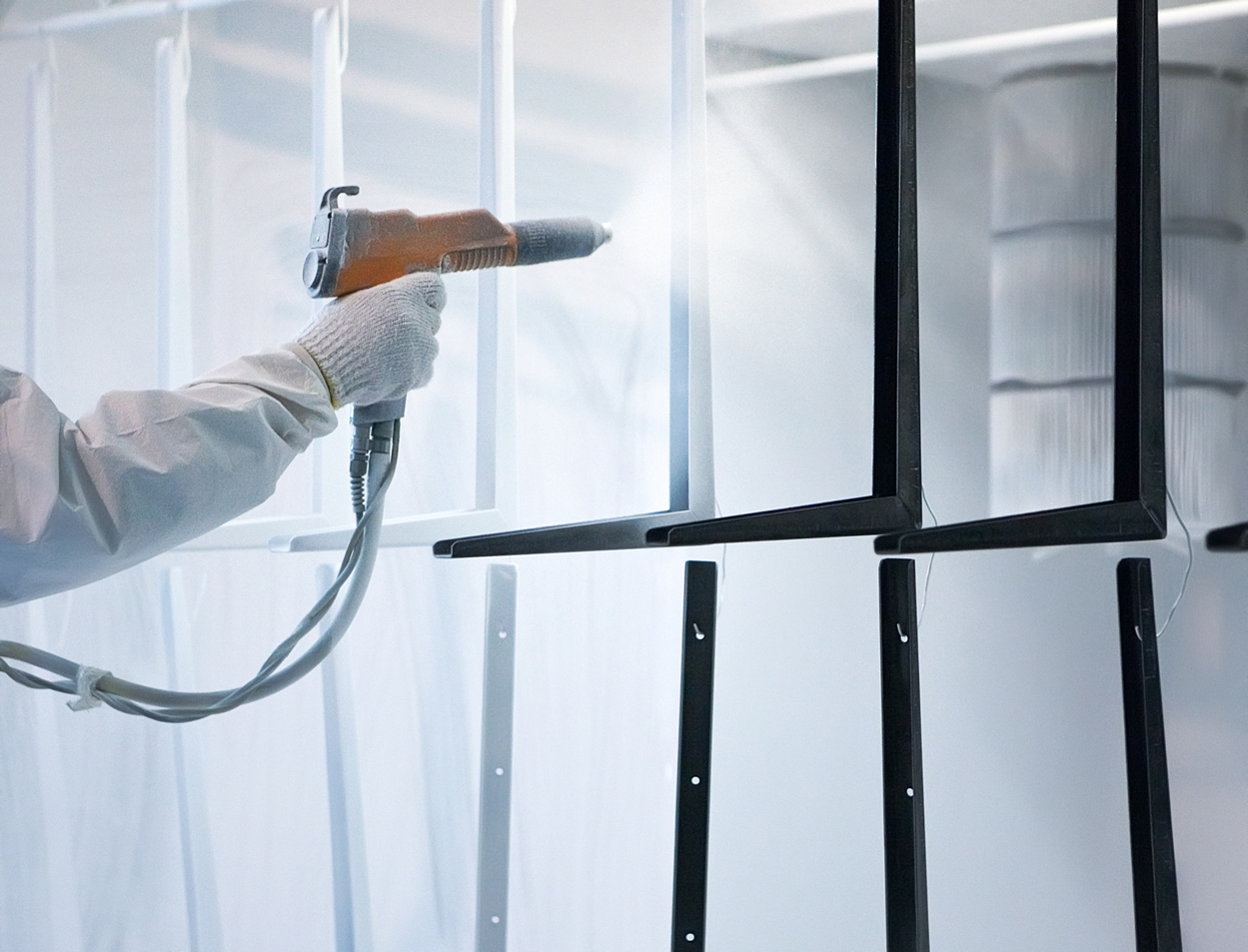


Deburr Finishing
Deburr Finishing is the process of creating an excellent surface finish for components before being powder coated or packaged to be dispatched to customers.

The Lazenby Group goes the extra mile to create the best quality products. Deburr finishing is made up of several different processes to create the best surface finish, including grinding, polishing, buffing and the use of a deburr linisher machine.
The Timesaver 32 series deburring linisher machine is a great innovation, removing all burrs and creating a smooth surface finish once a part has been lasered, leaving the most exquisite finish.


Fastener Insertion
Threaded fasteners are used in conjunction with a threaded insert to join two or more parts.

The threaded insert is embedded onto the face of a component, which allows for easy assembly and a more aesthetic finish in some cases.
Lazenby’s offer several methods of fastener insertion with the use of a PEM serter, Avdel or even the application of stud welding to install the insert onto the face.
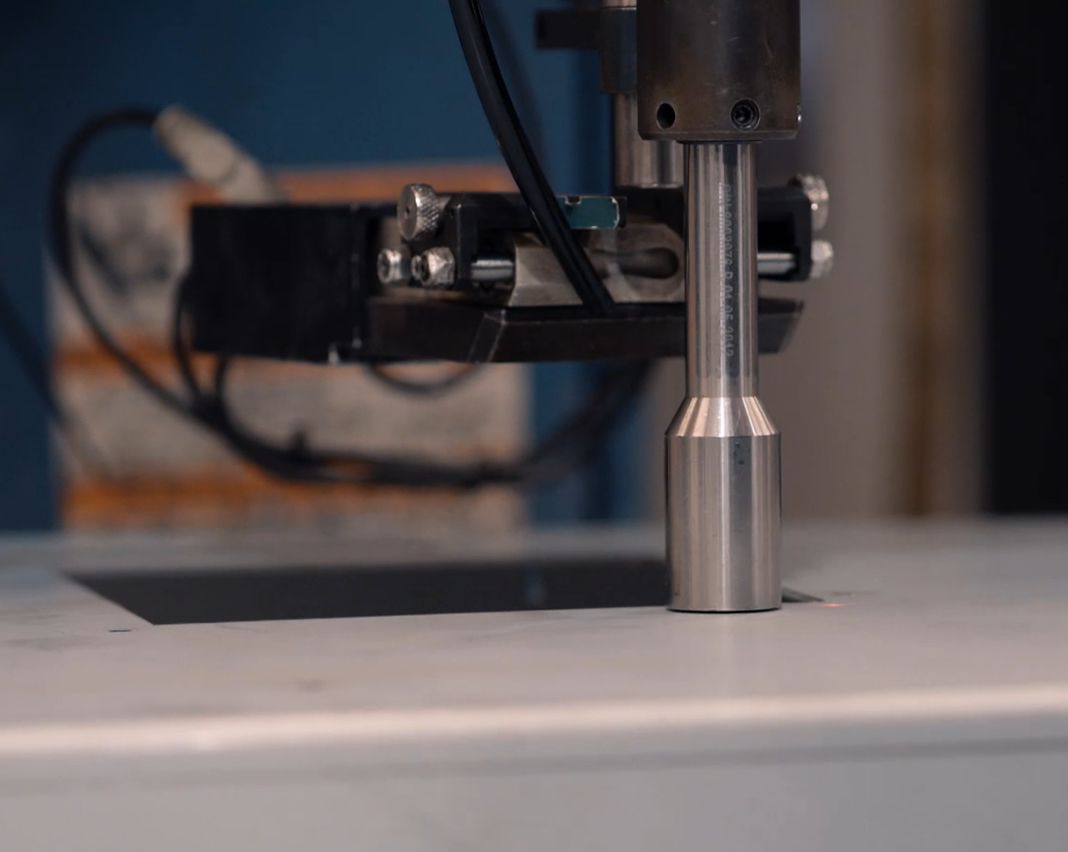


Additional Services
Additional Services are available at Lazenby's, including:

Guillotine Cutting
Sheet Metal Rolling
Drilling
Assembling
Packaging
3D Printing

What our customers say
about our company
Frequently Asked Questions
Why choose The Lazenby Group?
To ensure that we achieve the highest standard of fabrication possible, every stage of the manufacturing process is diligently checked and inspected, from initial design right through to production of the finished project, and again before being dispatched. Even the smallest details are accounted for, and everything must be checked twice to ensure the highest quality result. Quality control protocols and dimension measurement routines are put in place to ensure complete precision, ensuring that each process is executed with exacting attention to detail.
One of the main checks we perform before putting anything into production is to consider the material. The type of material you use can make all the difference to the quality. Before using any material, several factors have to be examined; including the purpose of the product, and any associated environmental issues.
Not only are the components thoroughly checked, but our machines must pass rigorous inspections as well to ensure that they are performing at optimum levels to deliver the highest quality. Checks are carried out daily before starting a task. In addition, complete inspections and tests are conducted on a regular basis by an external body, which are kept logged and dated. The quality checks of components are carried out by the shop floor employees, who are all highly trained and qualified engineers. Before anything is ever finalised, the factory manager checks the products before allowing them to be dispatched.
Below is a list of our sheet metal capabilities; however, if you need more information or have any questions relating to material capabilities, feel free to contact us so that we can discuss your requirements.
- Laser: Maximum sheet size is 3m X 1.5m, the maximum thickness depends on the material. The laser can cut the thickness of all the materials we work with here except plastisol. Please refer to the ‘What sheet metal materials do you offer to work with?’ FAQ for a list of materials.
- Punch: Maximum sheet size is 3m X 1.25m and maximum thickness is 3mm. The forming capabilities are dimple, vent, louvre and forming.
- Bending: Maximum length is 3m for materials up to 3mm and 1.5m for materials from 3mm to 6mm. Welding:MIG weld Mild Steel, Stainless Steel and Zintec. TIG weld Mild Steel, Stainless Steel, Aluminium and Zintec. Spot weld up to 3mm for Mild Steel, Stainless Steel and Zintec.
- Deburr Linisher Machine: Maximum thickness is 25mm and maximum width is 1.1m.
- Guillotine: Maximum thickness is 3mm and maximum length is 3m.
- Rollers: Maximum thickness is 6mm and maximum width is 1.5m.
- Bollof: Maximum thickness is 1.5mm.
- Studding: Use of PEM Serter, Avdel and Stud weld tools.
There are a wide range of processes involved in sheet metal fabrication, which are dependent on the required outcome. Our main processes are:
- Laser profiling: This is where our TruLaser 3030 machine cuts a profile with extremely smooth edges from a sheet. It follows the specific path to give you the profile you need. The waste sheet metal skeleton is then recycled.
- Punching: This is where a tool is forced through the sheet at high velocity causing the sheet to become perforated, profiled or formed. Repeating this process then creates the desired pattern.
- Bending: This is where a press brake machine applies tonnage of pressure to a sheet to achieve a desired angle with the help of different press brake tools.
- Welding: This occurs once the components have been through all the other processes (not all of them are always required). Components are joined together to form larger assemblies through a process of MIG, TIG or spot welding.
- Powder Coating: A type of finish coating that is applied as a free-flowing dry powder to give components the finished look. The powder is a mixture of ground resin particles and pigment, which is applied electrostatically and is then cured under heat between 200⁰C and 240⁰C.
- Deburr finishing: This is where the sheet is deburred of any sharp edges. The flat components go through our TIMESAVERS 32 series machine to remove burrs. Components also go through a stage of grinding, polishing and buffing to give them an excellent surface finish to then be sent to customers or before going to be powder coated.
- Fastener Insertion: This is where fasteners are embedded onto a component’s surface. Common fasteners that our machines press in are clinch nuts, clinch studs, weld nuts and weld studs.
There are some other additional processes which may take place during the course of a product being manufactured; for example guillotine cutting, drilling, assembling etc.
The materials we work with here at the Lazenby Group are:
- Mild Steel: 0.7-20mm (CR4 + HR4)
- Stainless Steel: 0.7-20mm
- Aluminium: 0.7-20mm
- Zintec: 0.7-3mm
- Copper: 0.7-8mm
- Brass: 0.7-8mm
- Plastisol: 0.7-1.5mm
- Galvanised: 0.7-4.0 mm
Feel free to get into contact with us if the material or thickness you require is not stated here; we may be able to cater to your needs.
Sheet metal fabrication provides many benefits and advantages. Sheet metals have great durability and malleability. They have a high strength relationship and are strong enough to withstand considerable pressures yet remain malleable.
They can be formed into many shapes, which allows for a wide range of innovative designs. They are recyclable, and sheet metals are resistant to natural threats but are not harmful to the environment. They can also have resistance to some corrosion with the right treatment. Sheet metals are light weight, unlike several other materials, making them highly portable and easy to handle.
They also offer great aesthetics; the seamless finish and options that are provided by sheet metalwork are unmatched. Not only do you get a seamless structure but the option for modification and painting makes it very beneficial.